HOW Warrior Sets the safety standards

Please click on circle to know more
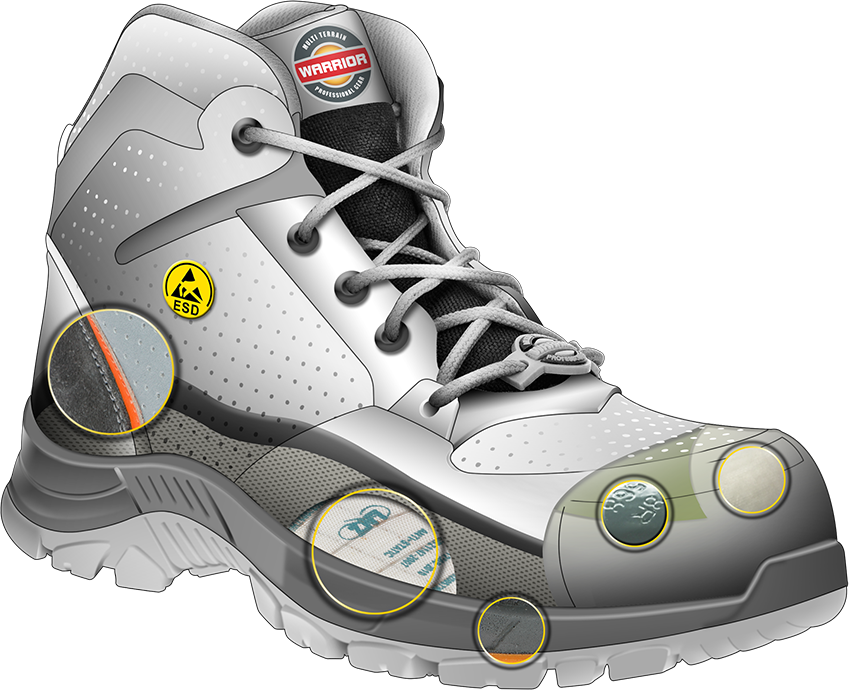

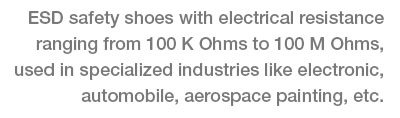
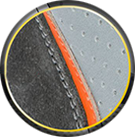
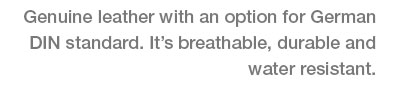
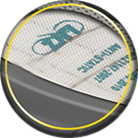
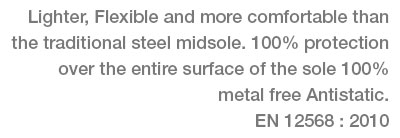

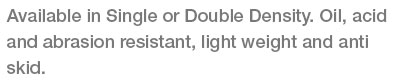

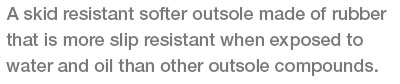

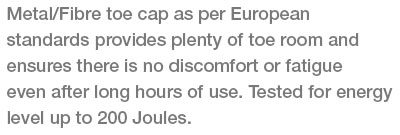

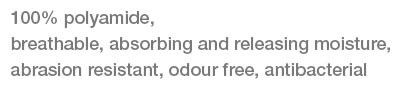
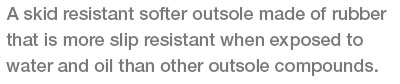
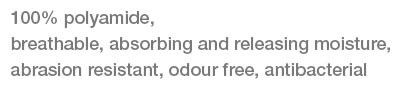
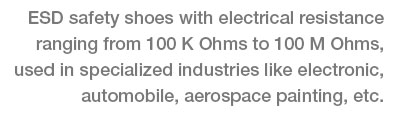
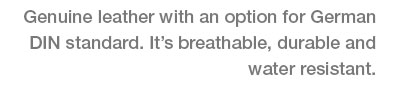
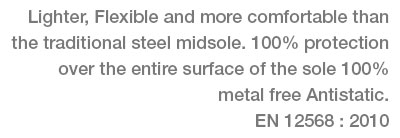
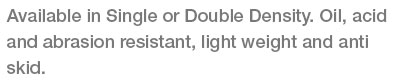
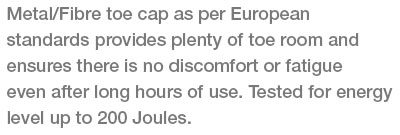
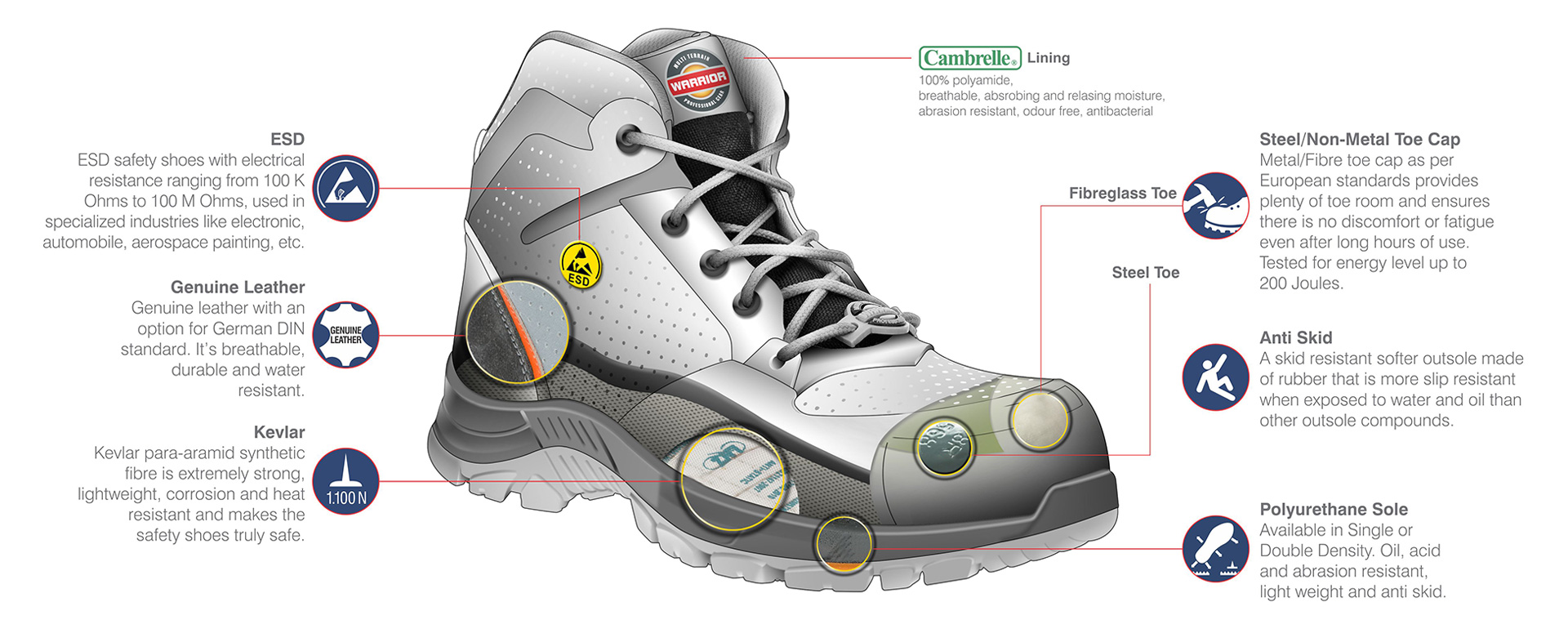
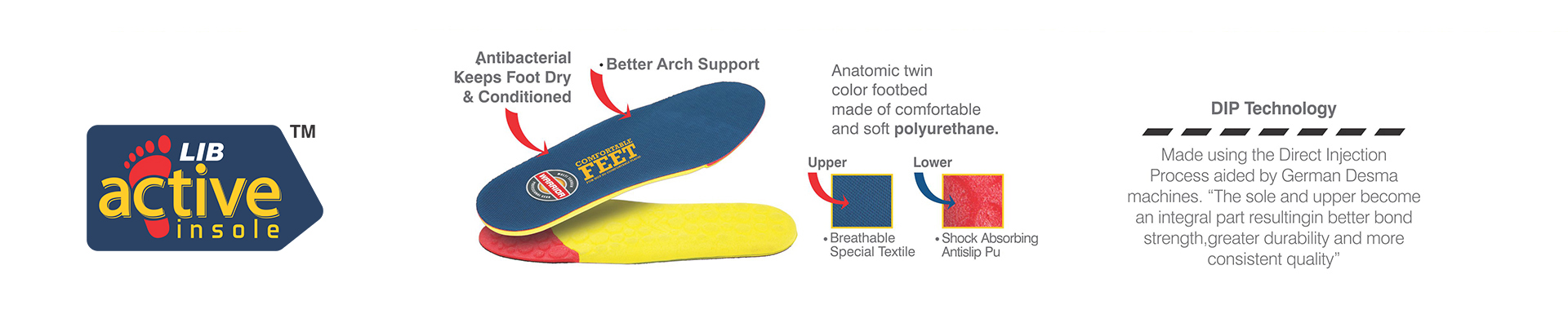
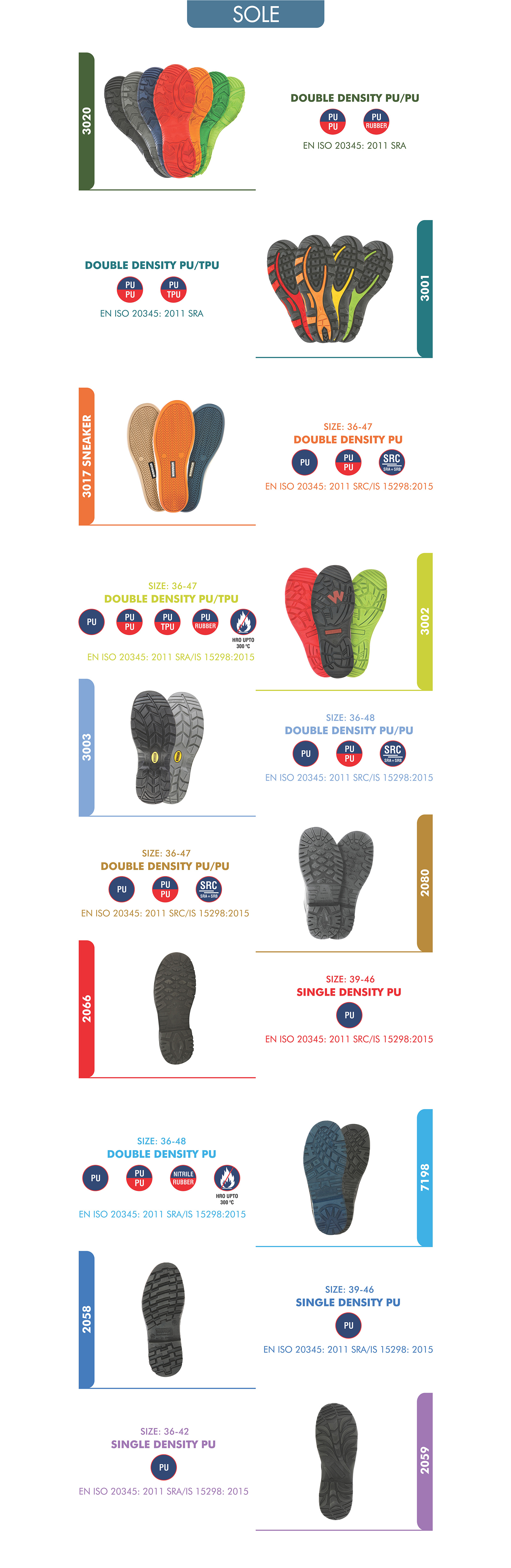
Materials
Uppers
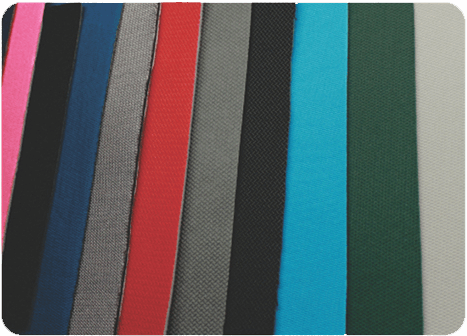
Leather & Microfibre
- 2.0 mm- 2.2 mm
- Full Grain
- Nubuck Special finish giving an authentic look
- Oil pull ups, Crazy horse
- Milled / Smooth Haircell
- Fine suedes
- Printed leather and microfiber as per customer requirement
- Special finish giving an authentic look. Water repellent and extra resistant to abrasion
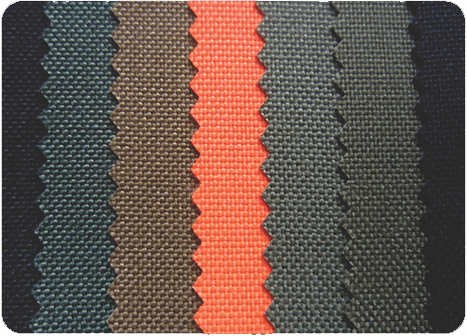
Cordura
- This fabric is used for certain parts of the upper or ankle of the shoes
- It is highly breathable with enhanced tear and abrasion resistance. Stylish durability with excellent strength to weight ratio
- Also used for soft inner lining applications with water repellant treatment and PU lamination technology
Linings
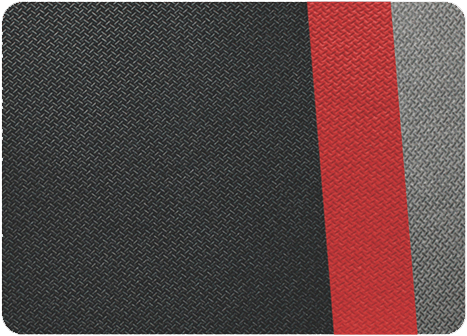
Cambrella
Cambrella lining offers greater comfort and hygiene. It is breathable, transferring humidity from the skin to the outside & highly resistant to abrasion. In the hot environment, we need protection against bacteria that cause odour. It helps to prevent the growth of bacteria too.
- Inhibit potential odours
- Minimize hidden stains
- Prolongs the life of footwear

Rice Mesh (Textile)
Breathable, absorbs and releases moisture, abrasion resistant
- Anti-slip
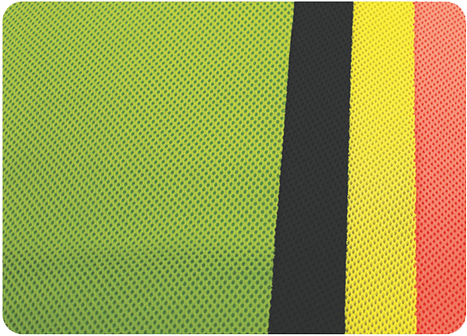
Spacer Fabric
Three dimensional (3D) textile, this is a particularly flexible and breathable lining. It ensures good ventilation to the foot and greater comfort.
- Delivers efficient stride
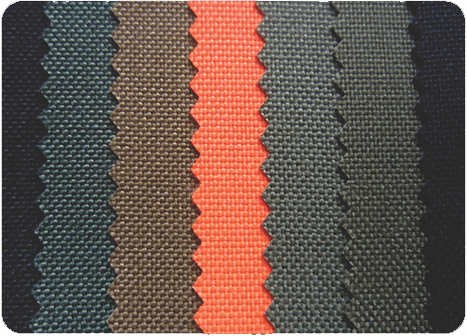
Water proof membranes
Provide unbeatable level of breathability. Transports moisture away from the body and at the same is waterproof. This quality of membranes makes it a different and excellent to be used in safety shoes.
- Anti-slip
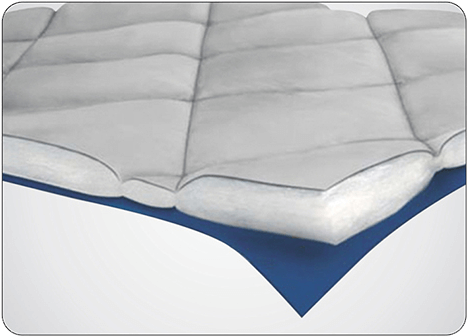
Thinsulate Insulation
THINSULATE Insulation 400g/ m2 and 600g/ m2 lining for extreme cold environments which will maintain body temperature.
- Delivers Efficient Stride
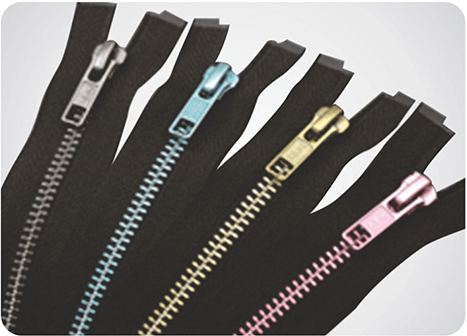
Zippers
100% polyester ribbons. All metal zips used in Warrior Safety Shoes are from YKK. Guarantee of long term resistance, smoothness and easy usage.
Toe caps and midsoles
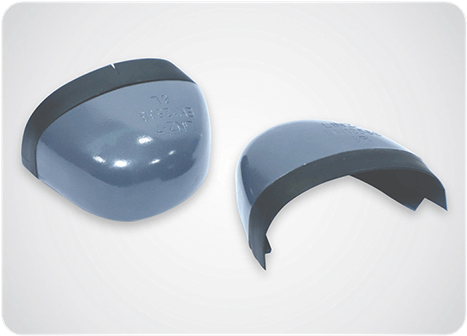
Fibreglass Toe Cap
Ultra-lightweight toe cap nonmagnetic thermal insulating EN 12568 : 2010
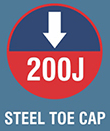
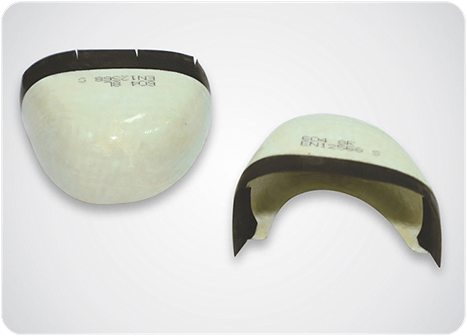
Fibreglass Toe Cap
Ultra-lightweight toe cap non-magnetic thermal insulating EN12568 : 2010
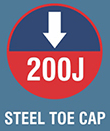
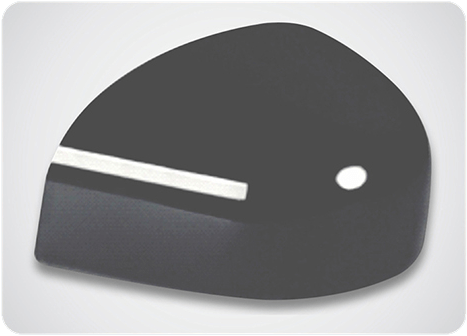
Aluminium Toe Cap
Very lightweight. Wide toe cap EN 12568 : 2010
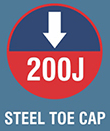
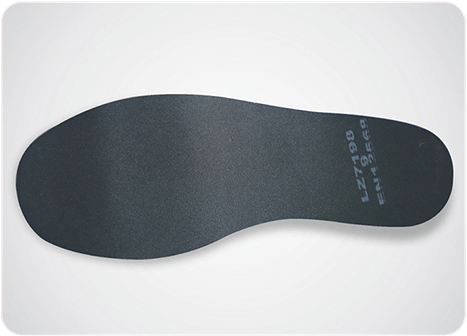
Steel Plate
The most effective protection against perforation EN 12568 : 2010
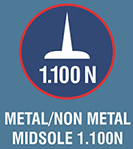
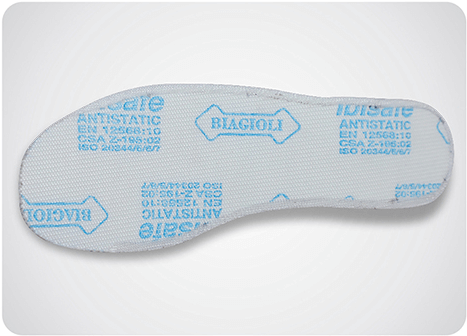
Kevlar- Anti Perforation Textile Midsole
Lighter and more comfortable than the traditional steel mid sole. Flexible. 100% protection over the entire surface of the sole. 100% metal free Zero Perforation Antistatic EN 12568 : 2010
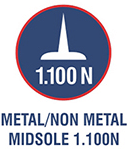
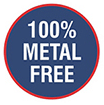
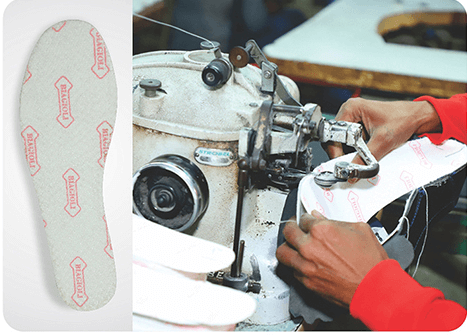
Imported Antistatic Strobel from Biagioli, Linz etc.
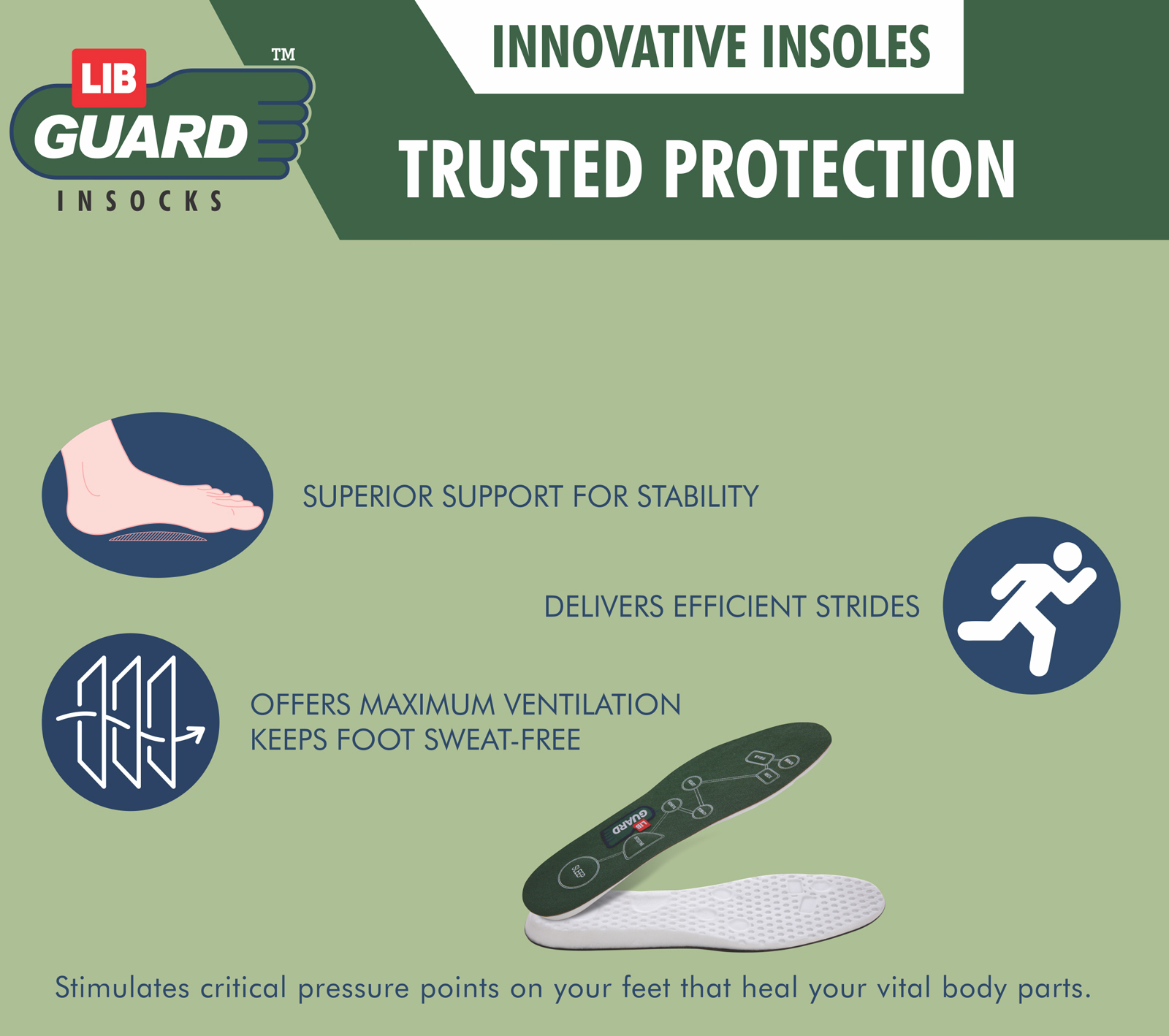
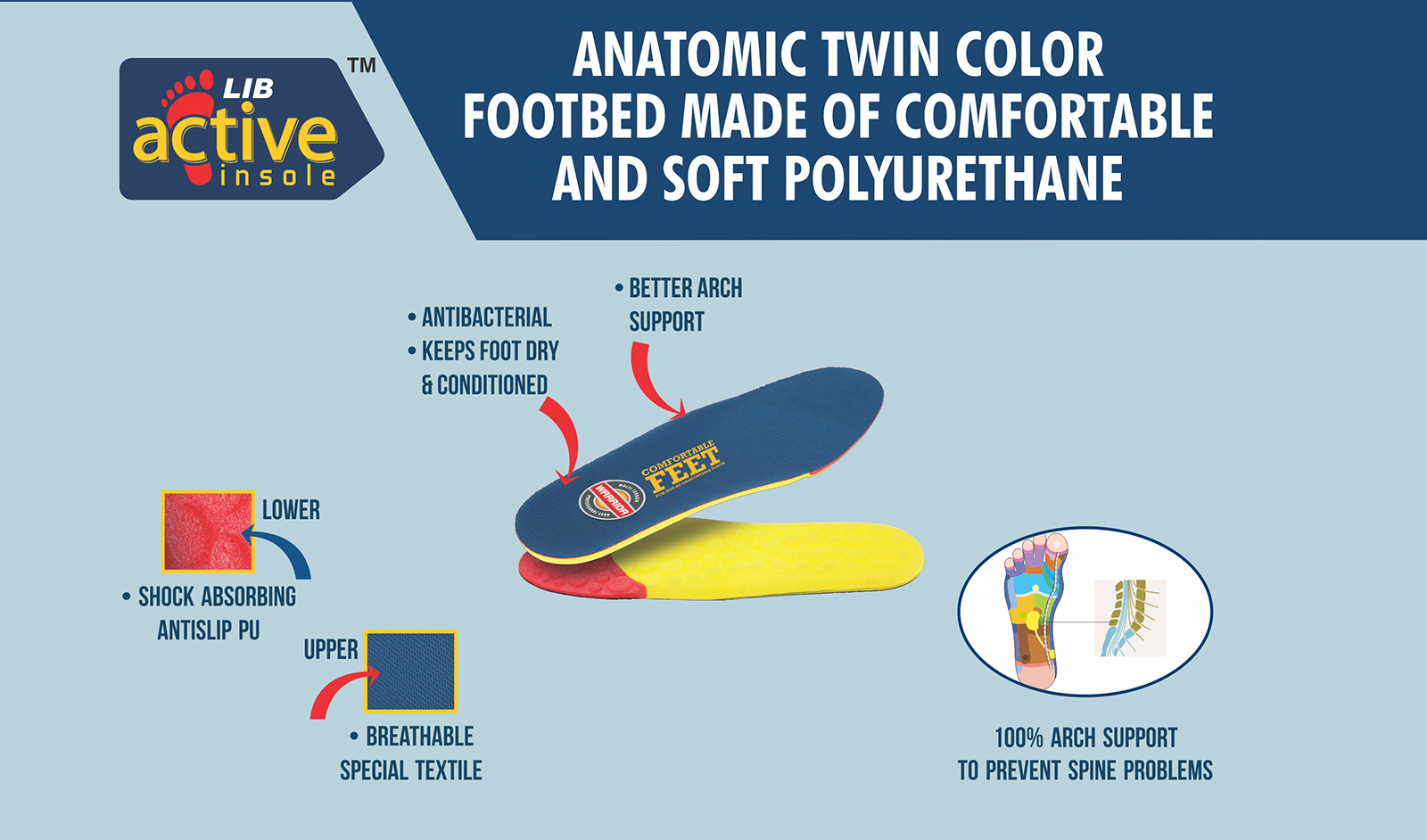
Production Process
DESIGNING & DEVELOPMENT
Designing and development department is equipped with latest CAD CAM software with 5 dedicated designers and a team of prototype sample maker. The designing team also includes technical persons to make the specification sheet of the product
TANNERY
A modern equipment with latest plant, machinery and technology capable of producing 400,000 Sq. ft of finished leather per month which includes Bovine (Buffalo, Cow), Sheep & Goat.
The plant is also equipped with a latest version of digital pollution treatment plant with direct online recording system for Liberty and Government controlling department.
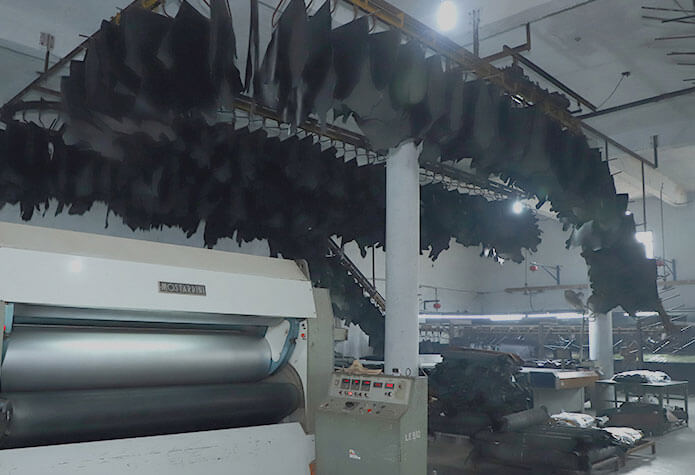
RAW MATERIAL STORE
A raw material store is spread over 10,000 sq .ft is connected to our ERP system with 10 digit code for each material identifying country of origin, material type, broad specification and detailed location for easy identification and traceability. The dedicated system of inventory management which includes MOQ (Min Order Quantity) and ROL (Re order level) is maintained for all types of materials.
CUTTING
Is equipped with 27 swing arm leather cutting machines 6 numbers of beam machines, splitting, skiving and stamping machines to handle a capacity of 100,000 pairs per month.
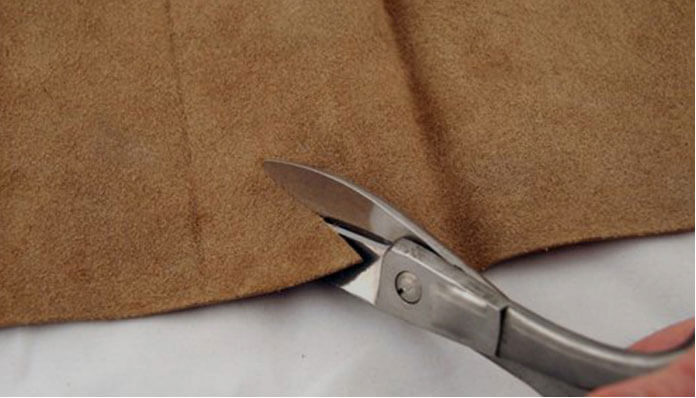
CLOSING
Besides 3 full-fledged in-house conveyors, a group of Liberty manages stitching fabrication units which are capable of manufacturing about 150,000 pair uppers per month.
STROBEL LASTING
With 10 numbers of strobel stitching machines and 7 numbers of lasting machines. The plant is equipped to manufacture 125,000 pairs of strobe led/lasted shoes with canvas/cellulose and Kevlar insole.
INJECTION
Having 5 numbers of DESMA direct injection machines (24 stations each) from Germany.
4 numbers of GUSBI machines with 60/40 stations for production of shoes, thongs, sandals etc.
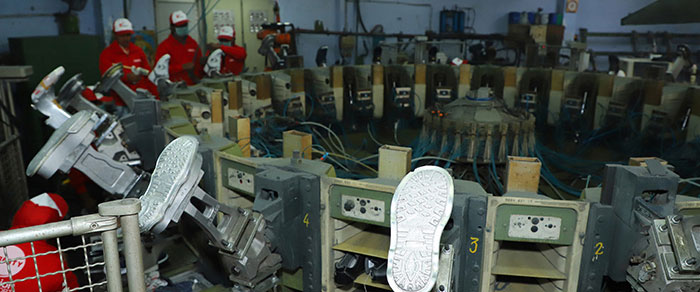
QUALITY CONTROL
Every process starting from raw material in different stage like cutting, closing, lasting injection. A team of educated and experienced quality inspectors inspect each component before it is passed on to the next stage. Records of such quality control are maintained and any deviation is directly brought to the management for immediate correction.
During direct injection samples of PU cup tests and tested soles are maintained for its traceability for more than 6 months.
Each pair of shoe has unique identification code to trace the exact date of production.
FINISHING AND PASSING
The plant is equipped with 5 conveyors lines for complete finishing of the shoes as per customer’s requirement and packed accordingly.
LABORATORY
- Is equipped with 48 types of testing equipment/ tools calibrated by external agencies on yearly basis for testing as per the latest norms of EN ISO 20345 : 2011 and BIS 15298
- Have 6 scientists/ technologists to test all incoming, in-process and finished goods.
- All input materials for store and leather are pre-tested and entered in the stock only when they pass the desired quality standards.
- Destructive tests of shoes are carried out to check the finished shoes as per EN ISO 20345 : 2011 and BIS 15298
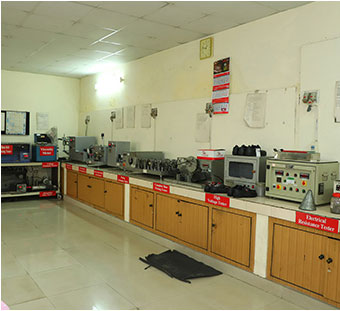
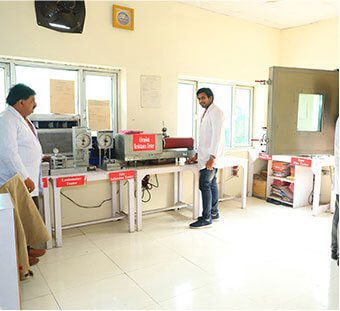
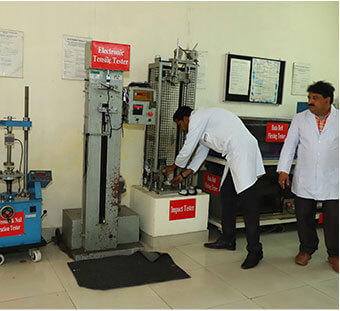
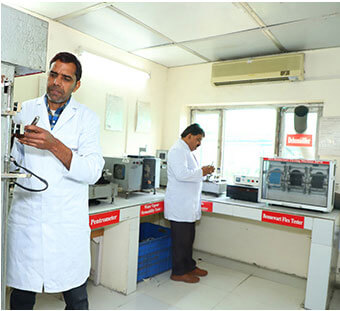
MANAGEMENT AUDIT FOR QUALITY
Before shipment of goods and expert critically inspects pairs selected at random (10%) to re-check that shoes meet the requirements of customers. Besides, the senior management team also checks the quality in process 50 times in a month in different departments to ensure that system is working as desired.
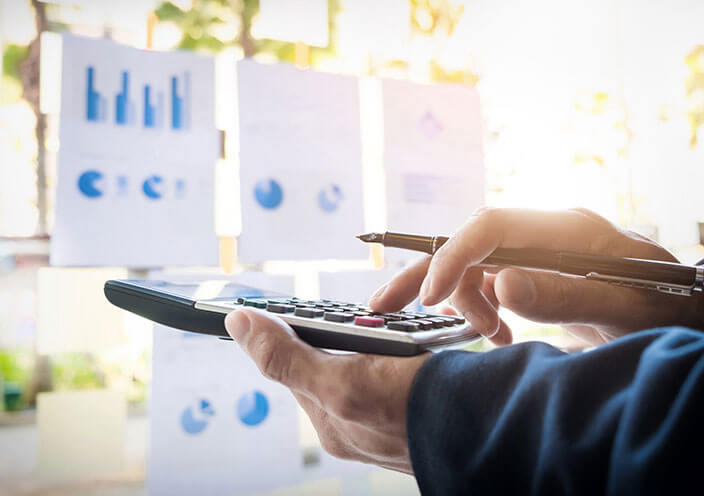
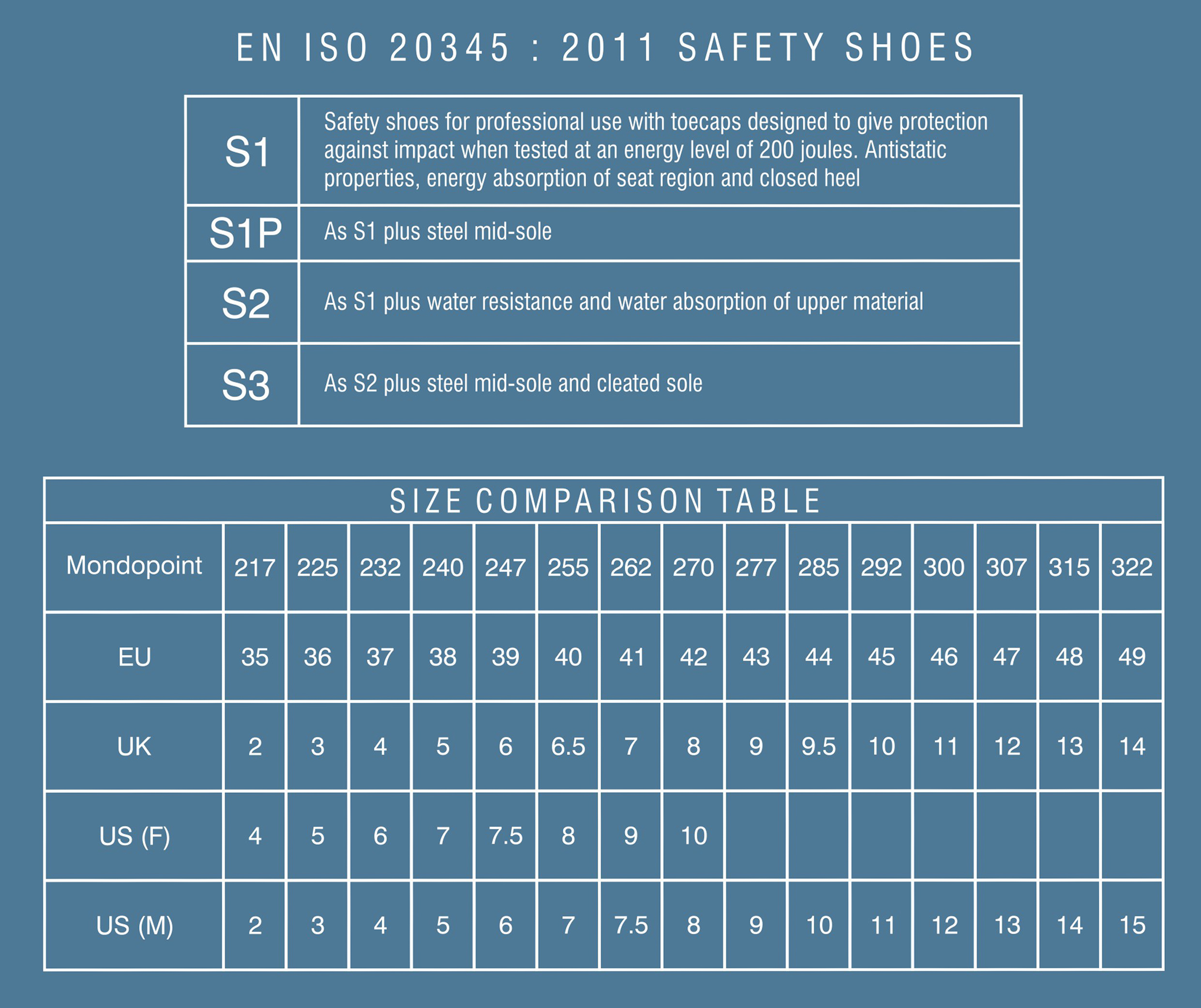